Aluminium Machining
Aluminium Machining in Shipley, West Yorkshire
At Development Engineering Services we are proud to be experts in aluminium machining for many customers across a wide range of sectors for over 25 years.
The benefits of using aluminium for CNC Machining purposes:
Strength-to-weight ratio
Many of our customers utilise aluminium because they require high strength to weight ratio, whereby the lighter weight of the material is important, particularly in the aerospace and subsea industries. However despite its lightweight, aluminium has very high strength and is cost effective versus other strong materials like titanium for example.
Surface finishing
The process of anodisation is a common surface finishing procedure which adds colour to the finish and additional corrosion resistance making this a popular choice amongst many industries who desire greater durability to their finished product.
High corrosion resistance
Aluminium is often favoured by industries due to its high corrosion resistance properties. The anodized layer makes the aluminium surface much harder than untreated aluminium, giving it enhanced resistance to scratches, wear, and corrosion. As a result, products made from anodized aluminium often have a longer lifespan, reducing the need for frequent replacements.
Where you have metals like magnesium that are too reactive they will oxidise easily and those less reactive like iron and steel will form a loose oxide layer such as rust. Here at Development Engineering Services we provide anodising as a surface finish.
Machinability
At Development Engineering Services we use aluminium across all of our machines utilising a variety of different manufacturing processes. Aluminium is an abundant material and works for both prototype and full production runs. It is a cost effective material as it is cheaper to buy and requires less power to machine than stainless steel for example. It can be cut quicker to tight tolerances and lends itself to precision machining due to the high accuracy levels we can achieve from manufacturing aluminium.
Recyclable and sustainable
Aluminium is a highly recyclable material and is therefore a sustainable material choice making it attractive to those who want to reduce material wastage. The process of aluminium manufacturing using a CNC machine generates a high volume of aluminium chips so it is good to know that these chips can be easily and quickly recycled.
Sub-zero temperatures
Aluminium retains its strength and ductility at sub-zero temperatures which is perfect for many of the industries we work with. Our customers often require components to go in to their finished products that are then used in very harsh conditions such as submarine and space.
Aluminium CNC Machining Processes
CNC milling and turning are the most common machining processes used in aluminium manufacturing that we provide here at Development Engineering Services.
CNC milling
CNC milling isa ‘subtractive’ (meaning material is removed) manufacturing process that combines traditional milling with computer numerical control (CNC) technology. CNC milling operations are the most commonly used in machining aluminium parts but can also be used to cut other materials like plastic and wood by using the rotating tool. We frequently use CNC milling to produce parts such as plates and housings for our customer base.
CNC milling is a fully automated process, whereby the machine’s movements are guided by pre-programmed code which dictates the toolpath, speed, and cutting depth, ensuring consistent and highly accurate results lending itself perfectly to manufacturing precision components.
CNC turning
In CNC turning, the workpiece rotates, unlike CNC milling whereby the workpiece is held stationary. As the workpiece rotates the cutting tool remains stationary and the tool is fed into the rotating workpiece to remove the desired material. This manufacturing process is used to create a cylindrical or conical shape that lends itself to producing rotational components for our customers. If the centre has both tuning and milling capabilities, the rotation can be stopped to allow for milling out of other shapes.
At Development Engineering Services, we have several different types of CNC machines that allow for varying levels of complexity in the cutting process. You can view our up-to-date plant list here.
Please do not hesitate to give us a call on 01274 595 808. We would be delighted to speak to you whether you have a potential project in the pipeline or you are just looking for some advice on any aspect of manufacturing. Our experts are on hand to help.
Our Plant
See our plant list, featuring state-of-the-art machinery and software, including ERP systems and offline programming, ensuring exceptional quality.
Plant List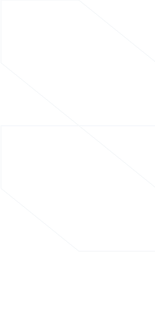
Our Sectors
Contact us today
Please do not hesitate to contact us as we would be delighted to help you.
Phone: 01274 595 808
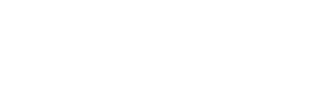
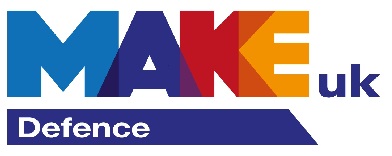
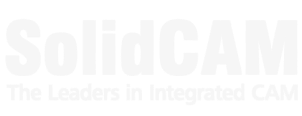
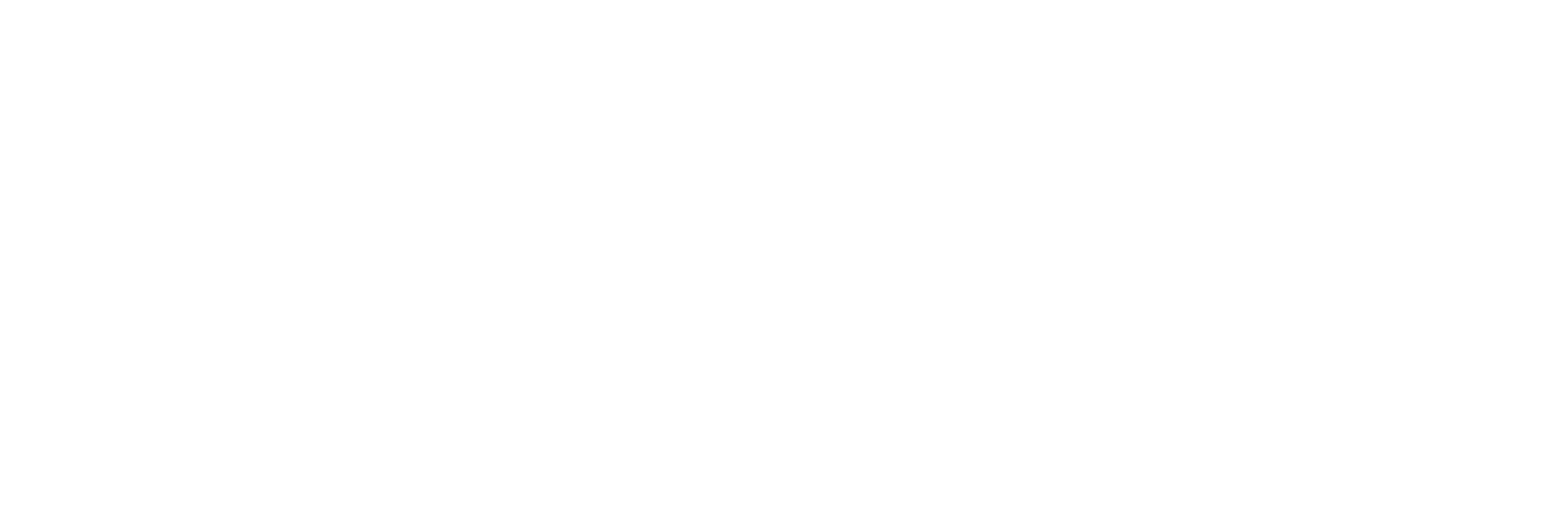
The values that drive everything we do
01
Re-investment
Investing in DES from purchasing new machinery and tooling to supporting our small team provides our customers with high quality products and great service.
02
Innovation
Using our experience and expertise to offer new ideas and improve machining efficiencies for the customer wherever possible.
03
Collaboration
Always working in partnership with our customer’s engineering teams to deliver their required final product.
04
Quality
Our top priority is the quality of the finished product. Always inspected rigorously before delivering to our customers.
05
Integrity
Some of our customers have been coming back to DES for over 20 years. Read some of our 5 star customer reviews.